AUTOMOCIÓN
La IA se asienta en la fábrica de Renault en Valladolid
La factoría vallisoletana, donde 'nacen' 900 vehículos al día, concentra el polo de hibridación de la marca francesa junto a la industria de Palencia al producir los modelos Espace, Austral, Rafale, Symbioz y Captur
Symbioz, el último ejemplar de Renault y que se fabrica en exclusiva en Valladolid, alcanza los 500 pedidos tras dos meses de su lanzamiento
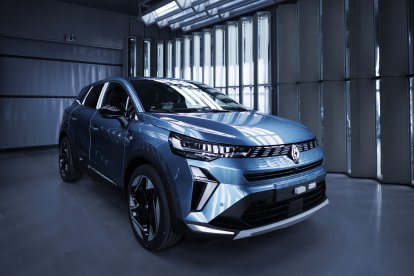
Imagen de la factoría de Renault Valladolid
Una reluciente flota de vehículos protegen las oficinas centrales de Renault en Valladolid. Distintas carrocerías, diferentes colores y nombres independientes -Austral, Espace, Rafale, Captur, Symbioz, Clio y Arkana-. que se se entremezclan con un rasgo en común: la motorización híbrida con la que el grupo francés se ha convertido en la segunda marca del mercado español con más ventas de este grupo de vehículos.
El distintivo ‘made in Spain’ predomina, aunque no visualmente, en en la gama híbrida de Renault. Y si el mapa es más exacto, Castilla y León es el verdadero ‘corazón’ del polo de hibridación de la compañía al producirse cinco de esos siete vehículos entre las factorías de Valladolid, donde ‘nacen’ los modelos Nuevo Captur y Symbioz, y de Palencia, con el Austral, Espace y Nuevo Rafale.
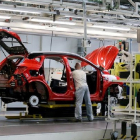
Negocios CyL
Subvención para la fundación UVA para prácticas en Renault y Horse
Diario de Valladolid | El Mundo
«En el año 2020 presentamos el cuarto plan industrial de Renault Group en España, que incluía cinco nuevos vehículos para las plantas españolas. Y esta foto -en referencia a los coches mencionados- demuestra que cumplimos nuestras promesas», destacaba Mercedes García, directora de comunicación de Renault Group Iberia.
Una historia de 70 años avalan las declaraciones de García, y sin pisar el freno, la confianza del grupo en el país sigue aumentando como demuestra que la línea de producción del Symbioz se realice en la Factoría de Valladolid, lo que supone su entrada en el segmento C. Y lo mismo sucede con la fábrica de Renault en Palencia, donde el lanzamiento del Rafale supone su aterrizaje en el segmento D. «Es la primera vez que Renault Group confía a una planta española la fabricación de un vehículo de alta gama», aseveró al respecto la directora de comunicación.
La avalancha de nuevos productos ha permitido a las factorías españolas aumentar su producción un 18% en 2023. Industrias posicionadas «a la vanguardia» al erigirse sobre las «patas» de la innovación, digitalización y descarbonización. Pero también gracias a la «calidad» ya que, según apuntó García, las fábricas españolas de Renault «siempre han tenido unos índices muy positivos de calidad, pero aún así, la llegada de nuevos productos enfatizan seguir trabajando en ella, con lo cual se han puesto en marcha una serie de mecanismos para todavía ser más exigentes en el cumplimiento de calidad premium que tienen los vehículos de nuestras plantas».
Entre las cuatro fábricas de Renault asentadas en la Península Ibérica, la de Valladolid es la que más protagonismo ha tenido en las últimas fechas con las llegadas del Nuevo Captur y Symbioz, con 1.200 y 500 pedidos, respectivamente. En las paredes de la planta quedan impregnados los recuerdos del Renault 5, aquel que revolucionó el mercado y con el que esta fábrica estrenó sus cadenas de producción allá por 1972 y tras ser inaugurada por el entonces príncipe don Juan Carlos. Y sólo dos años después llegaría el Renault 7, que alargó la versatilidad del R5 con el maletero que echaban de menos las familias españolas
Más de 8 millones de vehículos fabricados después, los nuevos tiempos exigen mantener el pie en el acelerador, y parece que esto se cumple al producirse actualmente un vehículo por cada minuto, mediante un trabajo conjunto por un equipo formado por 2.259 empleados e instalaciones robotizadas. Y, cómo no, la innovación, la digitalización y la descarbonización se observa en cada rincón de los edificios de chapa, pintura y montaje que integran la factoría vallisoletana.
Donde todo comienza
La Factoría de Carrocerías de Valladolid es donde comienza el despliegue de instrucciones del Symbioz y Nuevo Captur, en el departamento de Embutición e Inyección de Plásticos, con los procesos de fabricación de las piezas que componen el esqueleto del vehículo que pueden ser metálicas (acero) o plásticas, y que dan la forma al coche una vez ensambladas en la factoría de vehículo.
Las piezas metálicas industrializadas en el departamento para ambos vehículos se realizan en diferentes líneas de fabricación existentes distribuidas en cuatro líneas de corte, doce de embutición muy automatizadas, otra de embutición en caliente y cinco de corte láser. En este proceso, se consiguen 137 piezas entre puertas, lados de caja o techos para ambos modelos.
Dentro de la misma planta se localiza un taller para trabajos sobre piezas inyectadas en plásticos, fundamentales de cara al estilo del vehículo y diseño final del mismo, se inyectarán un total de 10 piezas para Captur y Symbioz, que conforman los paragolpes y portones traseros de los vehículos.
Asimismo, en esta localización tiene lugar el ensamblado de las baterías del polo de hibridación, y para ello dispone de la última tecnología para el ensamblado de baterías eléctricas de tracción para vehículos híbridos, con un proceso diseñado para asegurar la máxima seguridad y calidad del producto.
Cada vehículo lleva más de 3.500 puntos de soldadura, de los cuales el 78,8% se realizarán en el departamento de Chapa de la Factoría de Valladolid, donde 119 autómatas y 770 robots, de manutención y soldadura, unirán mediante diferentes tecnologías de ensamblado todas las referencias necesarias para montar una carrocería completa.
Un taller, el de Chapa, al que la digitalización y la Inteligencia Artificial (IA) ha llegado con proyectos como Bin picking, abastecimiento a los robots con AGVs que alimentan el contenedor consiguiendo 0-touch; cámaras 3D que hacen diferentes medidas cada una para que la soldadura láser del techo quede perfecta; cámaras de IA para la detección de la diversidad de piezas y para controles de calidad en tiempo real; el sistema RFID en mantenimiento que asegura el stock de manera automática controlando el flujo de entrada y salida físico del almacén; el proyecto Bodyshop 360, capaz de compartir toda la info en tiempo real en teles; un sistema de alertas de los operarios que cuando tienen algo que remontar le llega un mensaje al reloj del comodín de la UET y luz adaptativa para los controles de calidad en función de la diversidad del vehículo.
En el departamento de chapa, por ejemplo, el 100% de los puntos de soldadura están automatizados; el control geométrico de calidad llamado ‘Perceptron’ por el que pasan el 100% de las cajas, cuenta con cuatro robots con cámaras incorporadas en sus extremos, que son capaces de medir, en dinámico, 116 cotas específicas y dimensionales; las pistolas láser al final del proceso aseguran los juegos y afloramientos de las puertas conforme a las exigencias del cliente y el control de aspecto y calidad antes de enviar cualquiera de las 54 diversidades de caja que se dirigen a pintura en el túnel de calidad premium instalado para los nuevos vehículos.
Mientras que, sobre la digitilización, hay que tener que en cuenta que la Factoría de Valladolid es una planta piloto del ‘Manufacturing 4.0.’ con más de 15.595 datos subidos a la nube cada segundo.
Asimismo, la entrada en vigor de la normativa GSR2 (General Safety Regulation) que regula la implementación de sistemas avanzados de asistencia al conductor (ADAS) ha hecho necesaria una nueva arquitectura electrónica en el vehículo llamada SWEET 400. La puesta en marcha de este nuevo sistema electrónico ha hecho necesaria la construcción y validación de más de 200 prototipos antes de la industrialización de Nuevo Captur y Symbioz.
Con esta nueva arquitectura electrónica todos los procesos de validación para los protocolos de comunicación entre calculadores han cambiado, siendo necesaria la reprogramación en todos los puestos afectados del taller de Montaje y la instalación de nuevos servidores de ciberseguridad.
Todas las referencias se montarán en poco más de 4 horas en el departamento de montaje, en la carrocería pintada que llega del departamento de pintura, para finalizar el proceso de producción de Nuevo Renault Captur y Symbioz.
Siete colores a elegir
El Taller de Pintura es el laboratorio de la fábrica, donde las condiciones de limpieza y el respeto del medioambiente, son un principio de base del proceso. El proceso de pintado se realiza en varias fases: limpieza manual de las piezas para eliminar posibles suciedades; limpieza des ionizante para retirar restos de polvo; flameado de las piezas mediante una llama que asegura la adherencia de la pintura; imprimación, capa de pintura que protege la superficie; aplicación de color y aplicación de barniz.
Un detalle a tener en cuenta de este departamento es que no tiene línea de aprestos, de forma que la Factoría de Valladolid es la única del Grupo que cuenta con el proceso 4wet, que permite aplicar las capas, una detrás de otra, con un único pase por el horno al final del proceso consiguiendo un importante ahorro de energía y una reducción de las emisiones COVs del proceso. Además, este taller ha realizado un importante plan de ruptura para la reducción del consumo energético, de forma que Renault ha conseguido un ahorro del 40% del consumo de gas y del 10% en electricidad en los últimos dos años.
Con siete colores a elegir para las carrocerías del Nuevo Captur y Symbioz, la calidad premium se asegura cuenta con un túnel de calidad en el que los operarios realizan un control exhaustivo de la pintura gracias a una iluminación especial y un túnel de detección automática, donde cada cámara realiza más de 1600 fotos/minuto, lo cual permite un control de calidad exhaustivo, asegurando la calidad superficial y el aspecto final de la pintura, recogiendo 65.000 fotos por vehículo gracias a 40 nuevas cámaras situadas a la entrada y salida del túnel. También se utiliza la inteligencia artificial para analizar estas imágenes.
Por último, una vez finalizado el proceso de producción una selección de vehículos de diferentes colores vuelven al departamento de pintura para pasar por el medio de supervisión ‘Cabine Lumiére’.
Mini ITV para el final
Una vez unida la pletina mecánica y la carrocería, el vehículo sigue avanzando por la línea de montaje instalando las puertas, ruedas, combustible y otros fluidos necesarios para el funcionamiento. Al final de la línea, el vehículo terminado arranca por primera vez.
En muy poco tiempo, el vehículo es sometido a una mini ITV, donde se comprobará que el funcionamiento es correcto. Todos los vehículos, el 100% son sometidos a pruebas en estático y dinámico, como son el ajuste de ruedas, el reglaje de haz de luz de faros y el de dirección, exámenes de aceleración y frenada, y la calibración de ADAS.
Un proceso extenso en 305.435 metros cuadrados construidosque, sin embargo, permite que la Factoría de Valladolid produzca 900 vehículos al día.
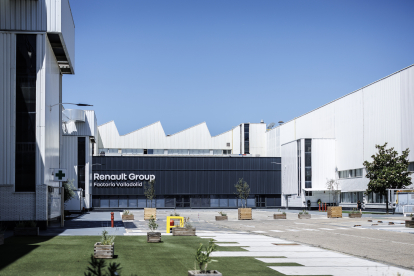
Imagen de la factoría de Renault Valladolid
Imagen de la factoría de Renault Valladolid
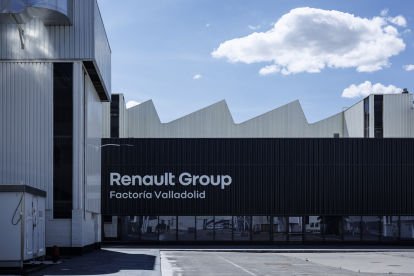
Imagen de la factoría de Renault Valladolid
Imagen de la factoría de Renault Valladolid
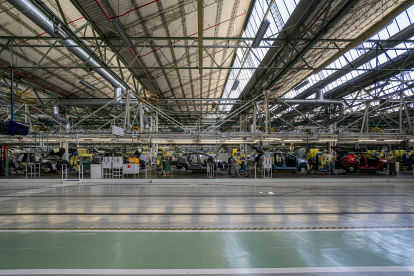
Imagen de la factoría de Renault Valladolid
Imagen de la factoría de Renault Valladolid
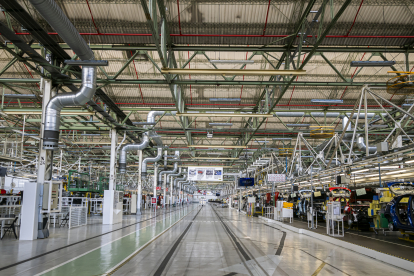
Imagen de la factoría de Renault Valladolid
Imagen de la factoría de Renault Valladolid
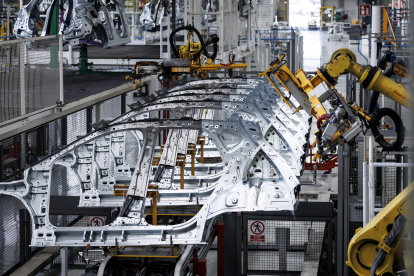
Imagen de la factoría de Renault Valladolid
Imagen de la factoría de Renault Valladolid
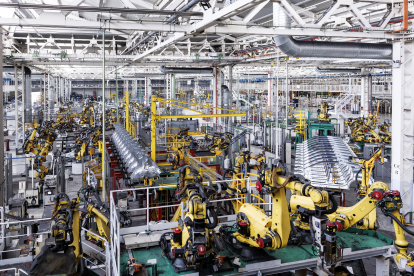
Imagen de la factoría de Renault Valladolid
Imagen de la factoría de Renault Valladolid
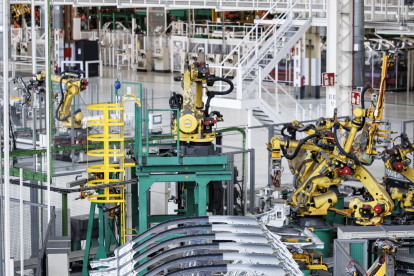
Imagen de la factoría de Renault Valladolid
Imagen de la factoría de Renault Valladolid
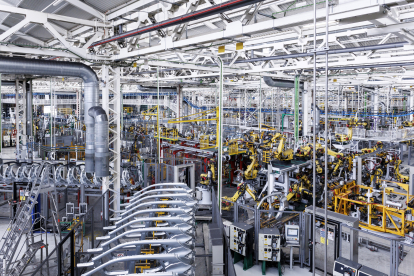
Imagen de la factoría de Renault Valladolid
Imagen de la factoría de Renault Valladolid
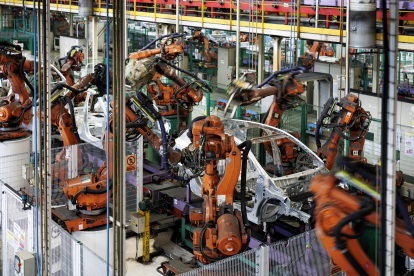
Imagen de la factoría de Renault Valladolid
Imagen de la factoría de Renault Valladolid
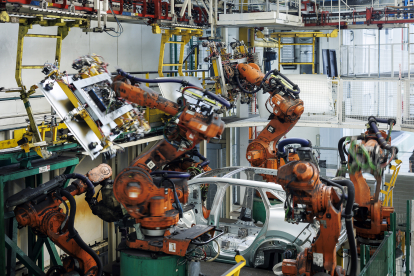
Imagen de la factoría de Renault Valladolid
Imagen de la factoría de Renault Valladolid
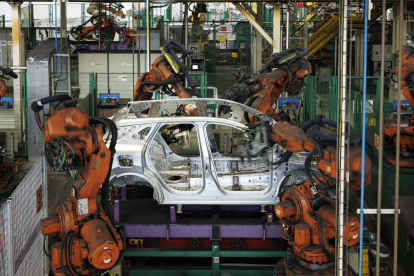
Imagen de la factoría de Renault Valladolid
Imagen de la factoría de Renault Valladolid
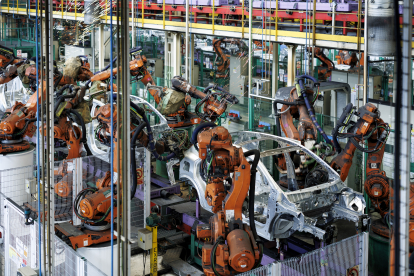
Imagen de la factoría de Renault Valladolid
Imagen de la factoría de Renault Valladolid
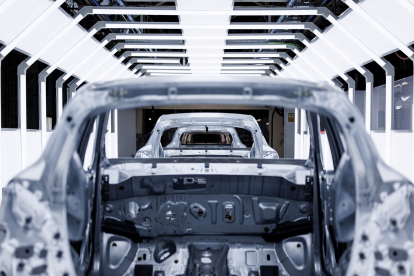
Imagen de la factoría de Renault Valladolid
Imagen de la factoría de Renault Valladolid
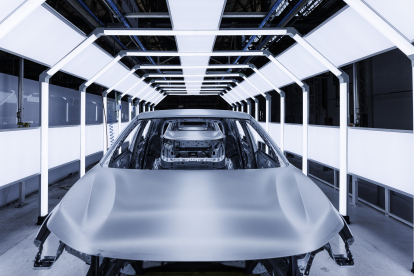
Imagen de la factoría de Renault Valladolid
Imagen de la factoría de Renault Valladolid
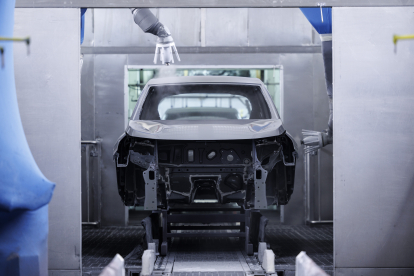
Imagen de la factoría de Renault Valladolid
Imagen de la factoría de Renault Valladolid
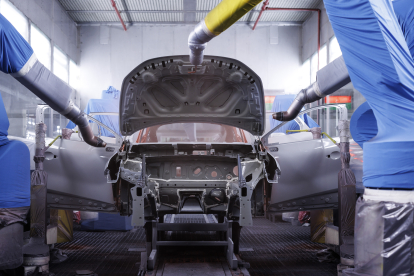
Imagen de la factoría de Renault Valladolid
Imagen de la factoría de Renault Valladolid
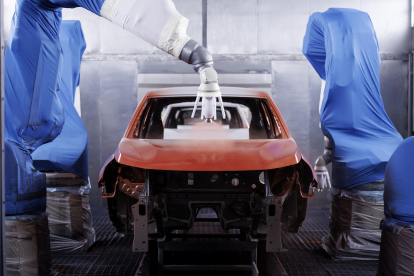
Imagen de la factoría de Renault Valladolid
Imagen de la factoría de Renault Valladolid
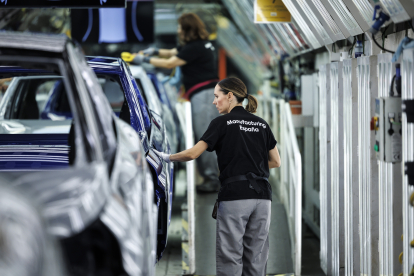
Imagen de la factoría de Renault Valladolid
Imagen de la factoría de Renault Valladolid
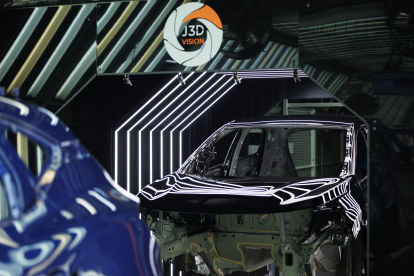
Imagen de la factoría de Renault Valladolid
Imagen de la factoría de Renault Valladolid

Imagen de la factoría de Renault Valladolid
Imagen de la factoría de Renault Valladolid
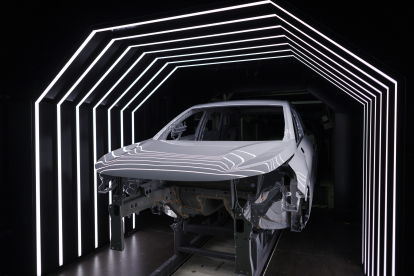
Imagen de la factoría de Renault Valladolid
Imagen de la factoría de Renault Valladolid
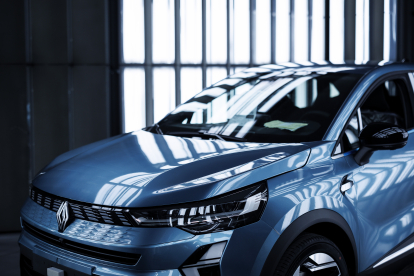
Imagen de la factoría de Renault Valladolid
Imagen de la factoría de Renault Valladolid
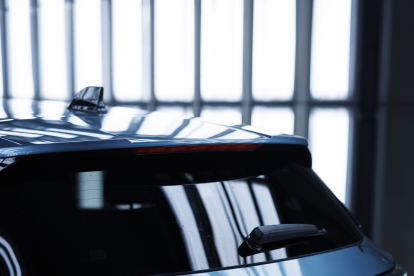
Imagen de la factoría de Renault Valladolid
Imagen de la factoría de Renault Valladolid
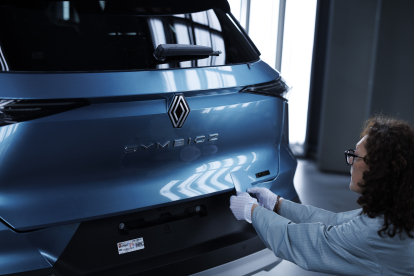
Imagen de la factoría de Renault Valladolid
Imagen de la factoría de Renault Valladolid
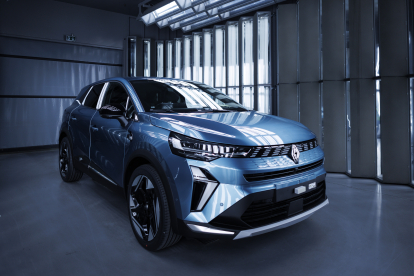
Imagen de la factoría de Renault Valladolid
Imagen de la factoría de Renault Valladolid
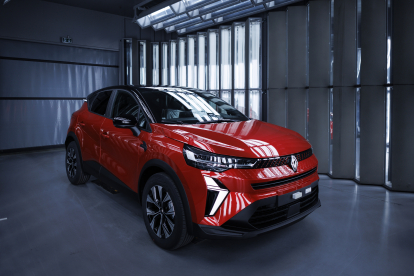
Imagen de la factoría de Renault Valladolid
Imagen de la factoría de Renault Valladolid
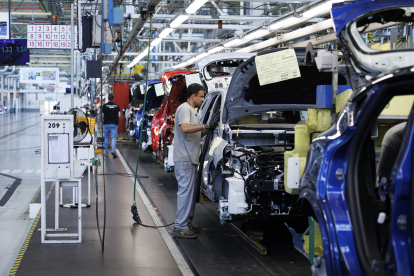
Imagen de la factoría de Renault Valladolid
Imagen de la factoría de Renault Valladolid
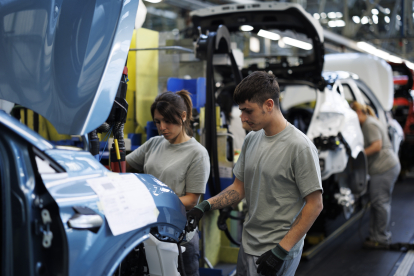
Imagen de la factoría de Renault Valladolid
Imagen de la factoría de Renault Valladolid
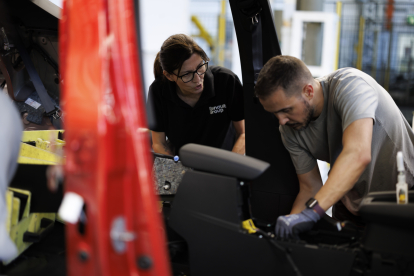
Imagen de la factoría de Renault Valladolid
Imagen de la factoría de Renault Valladolid
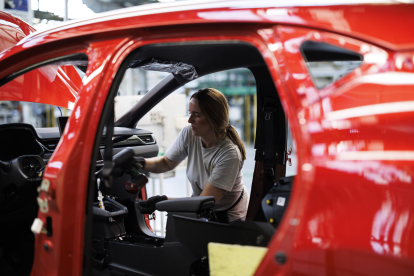
Imagen de la factoría de Renault Valladolid
Imagen de la factoría de Renault Valladolid
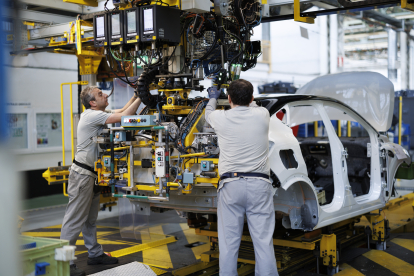
Imagen de la factoría de Renault Valladolid
Imagen de la factoría de Renault Valladolid
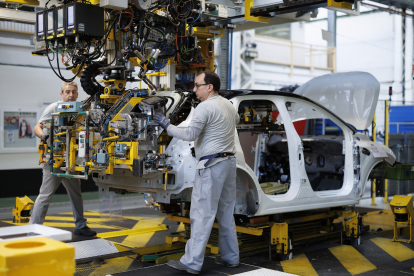
Imagen de la factoría de Renault Valladolid
Imagen de la factoría de Renault Valladolid

Imagen de la factoría de Renault Valladolid
Imagen de la factoría de Renault Valladolid
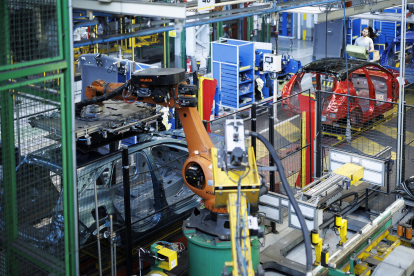
Imagen de la factoría de Renault Valladolid
Imagen de la factoría de Renault Valladolid
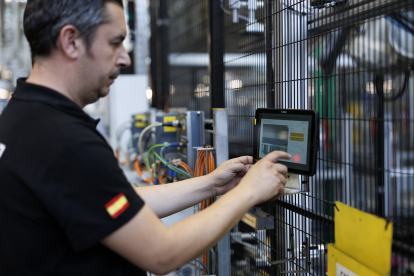
Imagen de la factoría de Renault Valladolid
Imagen de la factoría de Renault Valladolid
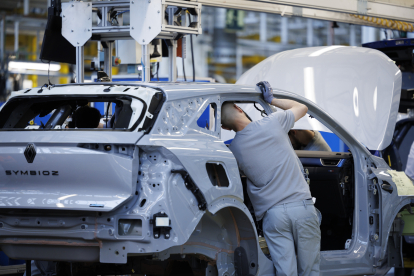
Imagen de la factoría de Renault Valladolid
Imagen de la factoría de Renault Valladolid
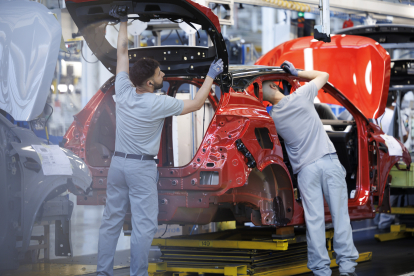
Imagen de la factoría de Renault Valladolid
Imagen de la factoría de Renault Valladolid
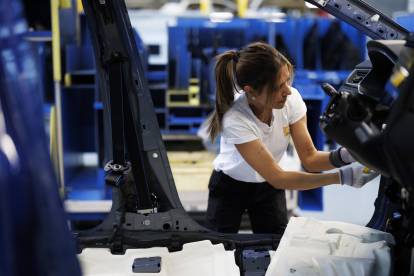
Imagen de la factoría de Renault Valladolid
Imagen de la factoría de Renault Valladolid
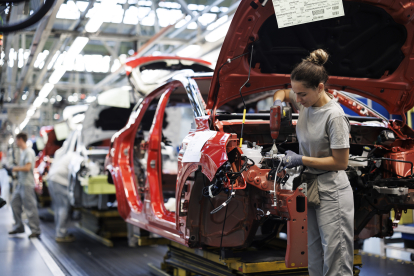
Imagen de la factoría de Renault Valladolid
Imagen de la factoría de Renault Valladolid
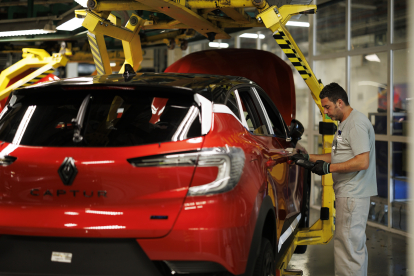
Imagen de la factoría de Renault Valladolid
Imagen de la factoría de Renault Valladolid
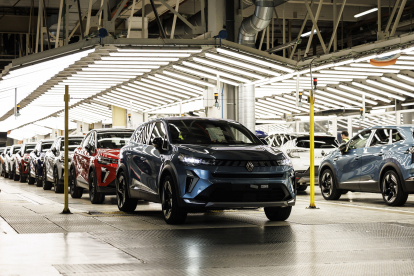
Imagen de la factoría de Renault Valladolid
Imagen de la factoría de Renault Valladolid
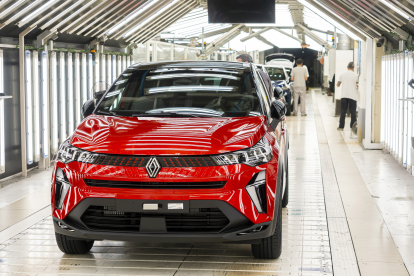
Imagen de la factoría de Renault Valladolid
Imagen de la factoría de Renault Valladolid
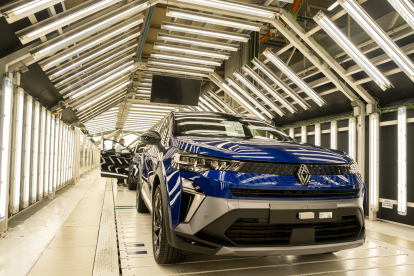
Imagen de la factoría de Renault Valladolid
Imagen de la factoría de Renault Valladolid
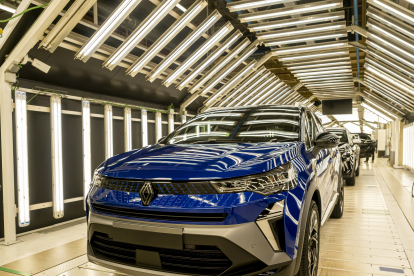
Imagen de la factoría de Renault Valladolid