Así será la fabricación del bus eléctrico de Switch en Valladolid
La cadena de montaje ocupará 'tres Zorrillas' y sacará tres vehículos cada quince horas / Su vida útil son 25 años, tendrá 15 puestos de soldadura y seis cabinas de pintura / Cada autobús estará compuesto por diez baterías en techo y trasera, dos transmisiones, 25 lunas y 1.200 tornillos y remaches
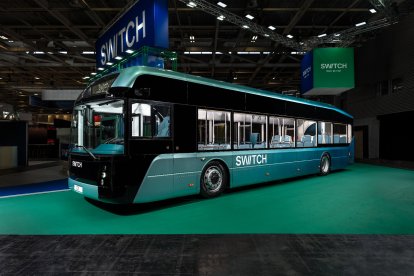
Presentación del nuevo autobús eléctrico que Switch Mobility fabricará en Valladolid. E. M.
Switch Mobility sacará tres autobuses eléctricos cada quince horas de producción. La cadena de montaje ocupará tres veces el césped del Zorrilla y tendrá casi tantos operarios como placas solares habrá en la cubierta de la nave. Funcionará durante 5.500 horas al año para producir algo más de mil vehículos por ejercicio. Eso será (si llega a establecerse en Valladolid, cuestionan los más incrédulos)cuando alcance su techo productivo, tres años después de entrar en funcionamiento, cosa que sucederá, como pronto, en 2025, más de un año después de lo previsto.
De momento, una certeza es que los proyectos técnicos para el desembarco se han sometido esta semana a información pública . El trámite es necesario para levantar las instalaciones en los antiguos terrenos de Acor y permite atisbar cómo será el proceso de fabricación de estos vehículos sostenibles. Dos documentos (el proyecto básico y el estudio de impacto ambiental) desgranan en más de 900 páginas los detalles de la futura planta y algunas curiosidades del futuro modelo de bus diseñado en exclusiva para los mercados europeos.
Desde la soldadura hasta los controles de calidad y posterior expedición del vehículo, la cadena de montaje se estructura en seis etapas, sin contar la fase preliminar.
Trabajos previos
Los camiones descargarán, a través de los muelles de carga, los materiales necesarios para el montaje. Se conservarán en un almacén general en el propio palet o en estantería, según las necesidades del proyecto, para su posterior suministro a las estaciones de trabajo. Los productos químicos y la pintura se conservarán en otro almacén específico.
La antesala de la cadena de producción contempla también los preparativos de las baterías y ejes . Según el proyecto, «las baterías se reciben en conjuntos estancos ensamblados por el proveedor, que se colocan en una estructura definida para tres subconjuntos traseros y sobre techo». Los dos circuitos de refrigeración se ensamblan separados y se dejan vacíos hasta el final del proceso.
Soldadura del chasis
La estructura del vehículo llegará de un proveedor del grupo en partes ya pintadas con pintura antióxido epoxi. La unión de los elementos se realizará en alguno de los quince puestos de soldadura previstos cuando se alcance la máxima capacidad. La zona contará también con tres columnas de aspiración y filtrado de humos o emisiones derivadas de la soldadura. Se trata de unidades con ventilador con capacidad para purificar 10.000 metros cúbicos por hora.
Una vez completadas las operaciones, se procederá al retoque de las zonas de unión de las partes en una cabina de pintura específica. En esta zona se localizará un puente grúa para manipulación de los elementos más pesados, con un monorraíl con capacidad para 3,2 toneladas.
Prepintura
Esta etapa contempla cinco estaciones. La primera es la mecánica, con la fijación del correspondiente sistema de frenado neumático y la columna de la dirección con la asistencia mecánica. A continuación se procede al cableado eléctrico. Continúa con los recubrimientos de fibra de vidrio interiores y exteriores, elementos que se fijan tanto con adhesivos como mecánicamente. Las placas de carrocería se fijan a continuación de forma mecánica remachándose. Luego se instala el sistema de climatización y ventilación . En esta zona se instalarán otros dos puentes grúa polipasto para manipular elementos pesados.
Pintura
Esta etapa estará delimitada por pantallas móviles para evitar suciedad en zonas aledañas, explica el proyecto. Primero se preparan todas las superficies mediante lijadoras orbitales con aspiración incorporada. El pintado incluye superficies metálicas, plásticas o de fibra de vidrio y mientras se realiza el proceso se aspira toda partícula de lijado evitando generación de emisiones difusas.
Con carácter previo, en el interior de la cabina de pintura se realiza la limpieza final mediante productos con bajo contenido de disolventes (estudio de productos para utilización de los que no cuenten con disolvente o tengan más bajo grado de disolvente). Los productos utilizados proceden de un almacén específico para el stock de pintura del tamaño de un dormitorio:unos 14 metros cuadrados. Allí se conservará la cantidad necesaria para tres días de fabricación, evitando la acumulación de grandes volúmenes dentro de las instalaciones.
Desde ese almacén, los materiales pasan a la ‘cocina de pintura’, donde se realizan las mezclas de base agua y disolvente con los colores necesarios para cada día de trabajo. La estación cuenta también con una lavadora para limpiar los equipos: se estima una necesidad de limpieza diaria de 30 pistolas.
Cuando ya se han ensamblado los componentes que conforman la estructura del autobús y se han preparado las superficies, el vehículo se introduce en una de las seis cabinas de pintura combi que habrá en la planta (en una primera fase sólo habrá dos), habitáculos estancos en cuyo interior se realizan las labores de pintura y secado.
Para acelerar el secado, las cabinas están equipadas con 56 paneles térmicos radiantes infrarrojos.
A continuación se procede al encerado de bajos del autobús en otra cabina específica, dotada con un sistema de elevación para acceder a la zona inferior del vehículo. El producto de encerado se almacena en el mismo almacén de pintura con un stock máximo de tres días de operativa.
Post-pintura
Una vez realizado el pintado, secado y encerado, el autobús atraviesa ocho estaciones donde se realizan varios procesos, como la terminación del suelo del vehículo, mediante uso de masilla de relleno, la instalación de ejes y ruedas, el ensamblado común de tornillería, la colocación de lunas y cristales del autobús mediante ensamblaje y fijación y actuaciones en cabina y los acabados interiores y luces.
Después se procede a la colocación de las baterías, pieza estrella de estos autobuses libres de emisiones . Primero, se instalan las baterías superiores con un puente grúa similar al utilizado en la zona de soldadura. Luego llega el turno de las baterías traseras, mediante un ‘ascensor’ parecido al de la cabina de encerado para elevar el vehículo.
Esta fase incluye también la instalación de los paneles de destino, los asientos y agarres , que se montan mecánicamente, así como el puesto del conductor.
Las estaciones posteriores incluyen el test eléctrico final del vehículo, los controles de calidad y el llenado de fluidos (refrigerante para baterías, limpiaparabrisas y gas de climatización). La puesta a punto prosigue con la alineación de ruedas y el test de frenado con los ajustes necesarios.
Control de estanqueidad
La penúltima etapa consiste en dar una potente ducha al autobús. Para probar su estanqueidad, se le somete durante un tiempo determinado a un flujo de agua que permitirá comprobar si existen fugas hacia el interior.
Situado el vehículo bajo seis arcos de salida del agua, la prueba consiste en verter sobre el autobús 4.500 litros de agua a una presión de dos bares, el ‘peso’ equivalente a bucear a diez metros de profundidad.
Expedición bajo pedido
La sexta y última parada del proceso productivo es el acabado y expedición de vehículos. No se prevé una gran zona de almacenamiento porque se trabajará bajo pedido. « Los autobuses se expedirán directamente a los clientes conforme a pedidos sin almacenamiento prolongado dentro las instalaciones», especifica el proyecto.
La nave de producción ocupará 21.170 metros cuadrados, el equivalente a tres veces el campo de José Zorrilla. Junto a ese bloque industrial, dentro del complejo, se adosarán a la fachada noreste dos núcleos de oficinas, donde se instalará la dirección y las zonas administrativas, con sus despachos y salas de reuniones, con 1.700 metros cuadrados distribuidos en tres niveles (planta baja, primera y segunda).
Tres años de crecimiento
La producción se incrementará de forma progresiva durante los tres años posteriores a su inauguración. Aunque los documentos fijan la apertura en 2024 y establecen la progresión para el trienio 2024-2027, la demora en la implantación obliga a retrasar por lo menos un ejercicio ese calendario. Será, pues, como pronto en 2028 cuando alcance su producción máxima para fabricar 1.091 autobuses al año. Para ello, la multinacional quiere atar un volumen de demanda mínimo que garantice la carga de trabajo necesaria para echar a andar y crecer.
Ese crecimiento de la actividad se plantea, en todo caso, en tres fases, con la instalación de otras tantas líneas de producción a lo largo de los tres años posteriores a la puesta en marcha de la factoría. En la primera fase se instalará una línea de producción con capacidad para ensamblar 150 vehículos al año. La etapa posterior contempla una segunda línea de fabricación que supondrá alcanzar los 820 autobuses dos años después. Al tercer año, la última fase dotará a la fábrica de su mayor nivel de producción, con tres líneas de montaje y una capacidad de sacar 1.091 autobuses anuales.
260 días de actividad, sin 'findes'
En cuanto al régimen de funcionamiento, se establecen 5.500 horas anuales de actividad cuando alcance su máximo ritmo, a los tres años de abrir, y hasta tres turnos de trabajo. Se estiman 260 días de funcionamiento al año, es decir, se excluyen los fines de semana de los 365 días que tiene el año.
Dado que a pleno rendimiento se sacarán más de un millar de vehículos al año en sus tres líneas de producción, se puede decir que de la factoría saldrá un autobús eléctrico cada quince horas de trabajo. O, lo que es lo mismo, que cada cinco horas funcionando la planta expedirá, de media, un vehículo.
10 baterías, 25 lunas y 1.200 tornillos
El vehículo que se va a producir en las instalaciones de Valladolid es un nuevo modelo diseñado en exclusiva para los mercados europeos por los equipos de I+D+i propios de Switch Mobility, ubicados en España con el apoyo de Reino Unido.
Cada autobús estará formado por 3.410 componentes, suministrados como productos acabados para su montaje y acopiados en el almacén general hasta su suministro. Es decir, la planta consumirá cada año 3,7 millones de piezas para ensamblar cada vehículo.
Una tabla enumera la lista de componentes. Así, cada autobús estará compuesto por dos transmisiones, diez baterías, 25 lunas, cuatro piezas para la climatización del habitáculo, 1.241 tornillos y remaches, 1.429 componentes electrónicos, entre otros.
7 directivos y 56 jefes de equipo
La multinacional, que introdujo los primeros autobuses eléctricos de fabricación británica en las carreteras de Londres en 2014, dispondrá de una plantilla compuesta por 1.554 personas , de las cuales 1.397 serán operarios. Habrá 56 jefes de equipo y el mismo número de inspectores. Doce personas se dedicarán al control de calidad , ocho a producción, cuatro a ingeniería, cuatro a mantenimiento, cinco a labores logísticas y cinco a tareas administrativas. El cuerpo directivo estará formado por siete personas.
Además de la fábrica de autobuses eléctricos, la multinacional contempla a medio plazo construir también aquí otra planta de furgonetas eléctricas y una de ensamblaje de seis baterías eléctricas, así como la creación de un centro tecnológico de investigación y desarrollo para la creación de nuevos productos. En total, una inversión de cien millones de euros en una década. El proyecto técnico no cuantifica los empleos indirectos que puede generar en esta primera fase la fábrica de autobuses pero la compañía los cifra en 7.000 cuando su despliegue alcance las otras dos patas del proyecto previstas. La capacidad total, para todas las fases, será de unos 5.800 vehículos anuales, según anunció la compañía.
40 empleos para las obras de construcción
La compañía colocó en marzo de 2022 la primera piedra de un proyecto que debía concluir a finales de aquel año. Desde entonces la obra está parada así que, con suerte, la futura planta entrará en funcionamiento con año y medio de retraso sobre lo previsto en inicio.
En este tiempo, la ejecución de las obras no ha avanzado sobre el terreno. Y el plazo previsto para la construcción de las instalaciones es de siete meses desde el inicio de los trabajos, según consta en el propio estudio de impacto ambiental.
La edificación de la factoría conllevará la creación de 40 empleos directos y otros 50 indirectos. «La demanda de mano de obra puede absorber población activa local desempleada y que desde las últimas décadas han estado emigrando hacia otros puntos de la región con mejores perspectivas laborales, o atraer mano de obra de otros lugares próximos», contextualiza.
25 años de vida útil
El proyecto establece una vida útil para las instalaciones de 25 años. « Una vez finalizada se procederá al desmantelamiento y retirada de todos los equipos, edificios y resto de obras ejecutadas, salvo que pudieran destinarse a un uso posterior», reza el documento. «A continuación, se restaurarán los terrenos afectados restableciendo la parcela a su estado original».
Con el sometimiento a información pública de los estudios técnicos, el pasado lunes se abrió el plazo de 30 días para presentar alegaciones. Este proceso continuará con una propuesta de resolución de la Junta, que finalizará en torno al primer trimestre del próximo año, 2024, según fuentes de la Consejería de Medio Ambiente.
De forma paralela, en este momento «el promotor también está recabando autorizaciones puramente municipales» y «está trabajando desde el punto de vista patrimonial, dado que la parcela tiene algunas cuestiones arqueológicas que está resolviendo », explican desde la Consejería de Medio Ambiente. «Resuelto todo esto, se puede construir», apostillan.
Del yacimiento al Museo
En octubre de 2022, la Consejería de Cultura dictó dos resoluciones de la Dirección General de Patrimonio para autorizar las actividades arqueológicas de excavación y construcción de la nave industrial por la presencia del yacimiento Soto de Medinilla.
Entre las medidas correctoras, para evitar la afección a este yacimiento de la Edad del Hierro, el promotor deberá realizar el control y excavaciones arqueológicas «con la prescripción de que en la zona de interferencia de la obra con el cenizal indígena en su borde meridional, se excavará la totalidad de la incidencia y la anchura del área de trabajo será de un mínimo de dos metros, tanto en este área como en el resto de posibles áreas de excavación derivadas del control arqueológico, abordando en cualquier caso la totalidad de la evidencia arqueológica».
Por esta causa, los trabajos se realizarán bajo la supervisión del arqueólogo del servicio territorial de Cultura de Valladolid y la arqueóloga del Servicio de Ordenación y Protección de la Dirección General de Patrimonio Cultural. De producirse algún hallazgo en el transcurso de los trabajos, deberá ser entregado en el Museo de Valladolid.